EBI Sees Increase in Utilities Requesting Information on IPB Sunshields
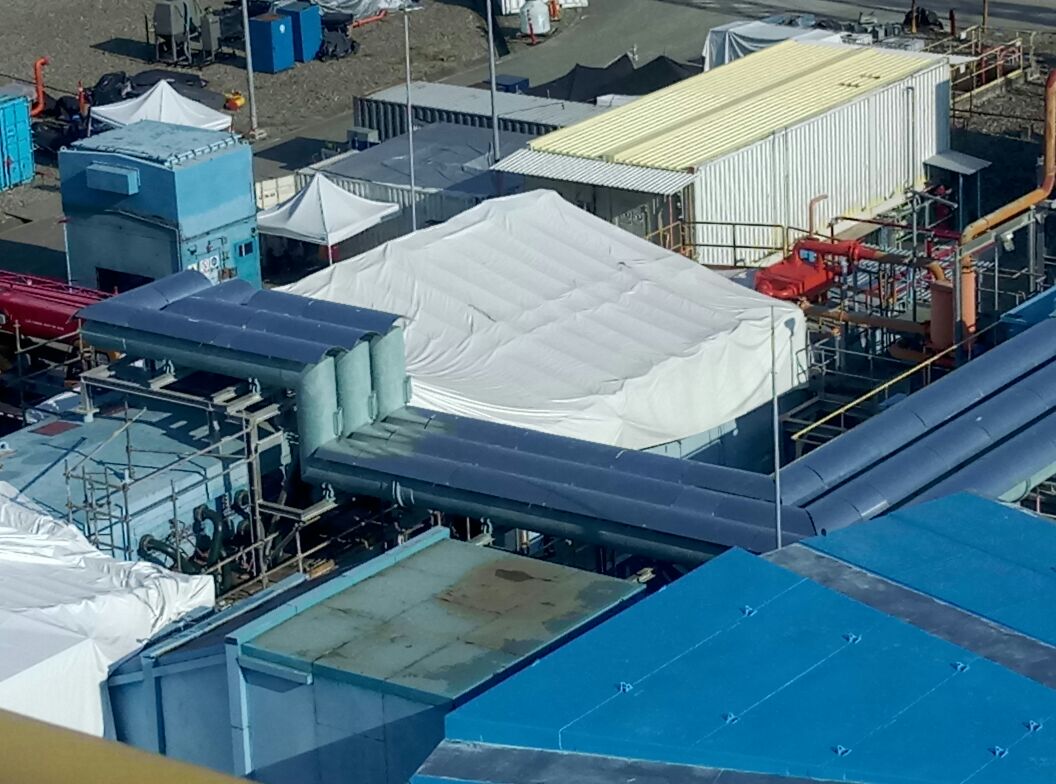
Over the past few years, EBI has received a growing number of calls regarding isolated phase bus (IPB) sunshields. Most commonly seen in foreign OEM bus duct designs, sunshields provide a shade or a canopy over the outdoor portion of the bus system in order to protect the enclosure from solar radiation caused by direct sunlight and to keep the conductor and enclosure temperature limitations established by the ANSI/IEEE C37.23 standard for metal enclosed bus systems. But why did sunshields enter the US marketplace in the first place? Quite simply, price!
According to the Electrical Power Engineering Reference & Applications Handbook, the normal practice of all leading bus duct manufacturers is to keep the same bus and enclosure sections for the outdoor and indoor portions of the bus system. This retains simplicity in the design and eases jointing and interconnections. However, this is also a costly arrangement since the indoor section of the bus system must be designed for outdoor conditions as well. Why?
The ANSI/IEEE C37.23 standard governs the temperature limitations for safe and effective operation of bus systems. Per this standard, the acceptable temperature for the IPB conductor and enclosure are 80°C and 105°C, respectively. Essentially, this allows for a 40°C and 65°C temperature rise over the ambient design temperature of 40°C for the conductor and enclosure. In very hot climate regions, the design ambient will be much higher than 40°C and maintaining the bus within the acceptable temperature limits will require a much larger bus design, resulting in the need for larger space and at a much higher cost when factoring in the additional material, shipping/handling, support steel, installation etc. As a workaround and to remain competitive worldwide, some overseas OEM manufacturers began offering the sun shielded IPB as a standard product, strictly for cost savings. With this method, the OEM can offer a smaller and less costly design and rely on the sunshields to accommodate the system temperature requirements.
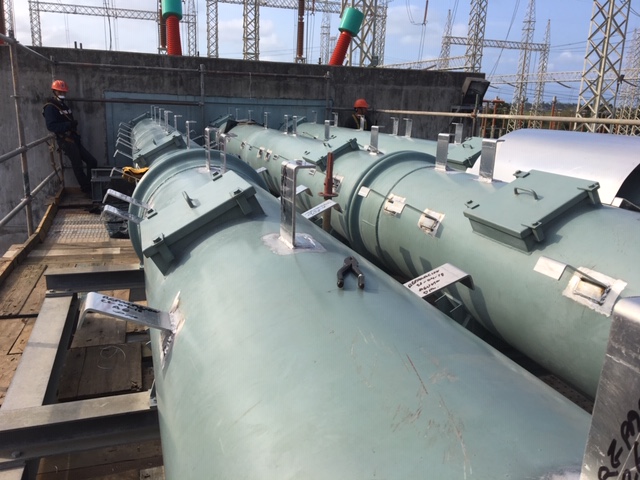
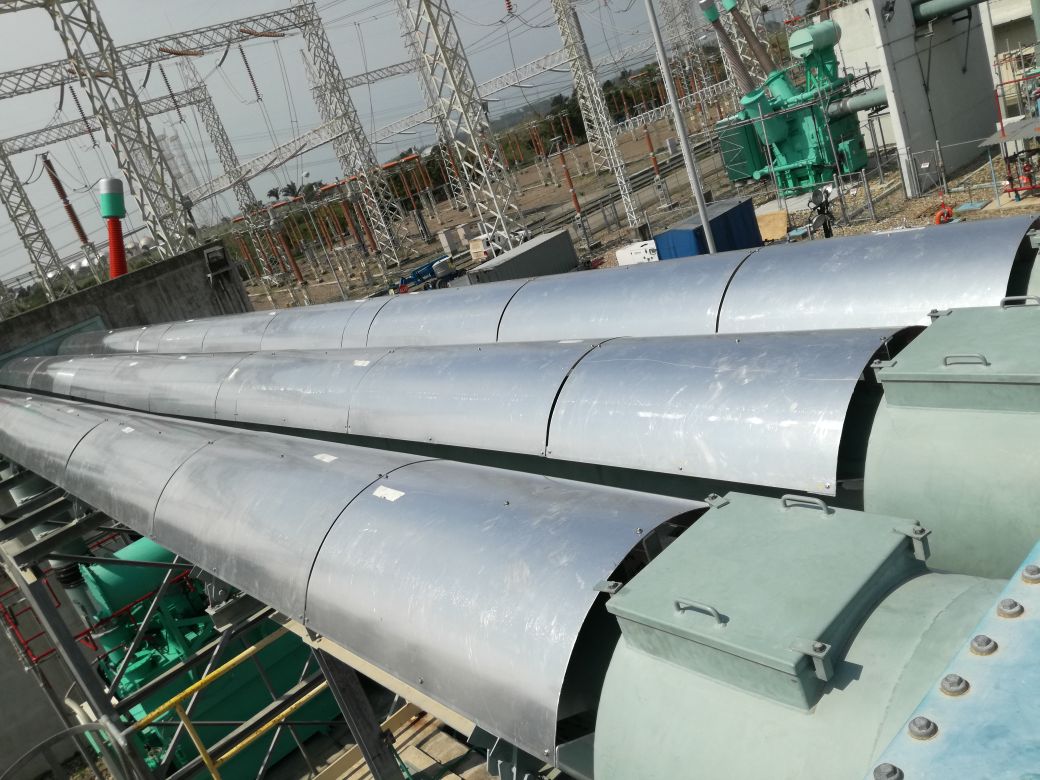
In certain instances, sunshields can also be retrofitted onto existing IPB bus systems. This is typically based on the potential of a minor uprate of the generator or the main transformer where the existing bus system is required to carry a larger amount of current. In such instances, instead of replacing the complete bus system at a significant expense, sunshields are added to the system. Naturally, incorporating sunshields into the scope must be based on performing a feasibility study which includes evaluating the available margins in the existing bus design as well as calculations to determine the amount of heat removal required during the highs of the day to assure the bus can withstand the new load requirements. Sunshields are typically designed in sections matching the enclosure diameter in either a half circle or roof top shape and welded at certain points above the enclosure. The section lengths vary but need to be designed to accommodate where expansion bellows are located in order to avoid damage to the shield welds in case of slight enclosure movement due to temperature fluctuations.

Like any other bus component, sunshields require periodic maintenance since they are subject to harsh environmental conditions. Some of the most common issues include material deterioration and weld breakage. In addition, the proximity of the shields to the bus enclosure could also cause some issues with heat entrapment and potential damage due to high winds. In short, installation of the shields must be performed by a qualified and experienced bus duct service provider, like EBI, and be part of an overall bus duct maintenance plan.
If you have questions regarding sunshield installation or are in need of sunshield repair, contact EBI at 877-297-0616.